Contact us
Tel: 021-68726200
15201970937 (Miss He)
Fax: 021-68726201
Address: building 2 (head office), no. 1279, east China road, pudong new area, Shanghai
Bearing industry
Information
One, introduction of bearing industry:
Bearing is a component which is used to determine the relative moving position of the rotating shaft and other parts, and plays a supporting or guiding role. Its performance, accuracy and reliability play a decisive role in the normal work of the main body.
China is a big country in bearing production, but compared with the bearing industrial power, China has a large gap, which is mainly characterized by high precision, high technology content and high value-added products, and the main products are satisfied by import. More than 75% of the global market share is concentrated in eight multinational bearing groups: SKF in Sweden, INA and FAG under the German skafer group, NSK, Ntine (NTN), KOYO, Minebea, Nachi, and Timken (TIMKEN) in the United States.
In addition, my domestic famous enterprises are: human group limited company, Wanxiang Limited by Share Ltd, Wafangdian City bearing Refco Group Ltd, Luoyang LYC Bearing Co., Ltd., Tianma Holding Group Co., Ltd., Zhejiang Wuzhou new spring group Co., Ltd., Dalian Metallurgical Bearing Group Co., Ltd. Hubei new torch group company, Harbin Bearing group, Shanghai Ji You machinery Limited by Share Ltd, Xiangyang automobile bearing Limited by Share Ltd, etc.
At present, the CBN grinding wheel is basically used in the foreign enterprises' products grinding, and the domestic enterprises are mainly the general corundum grinding wheel. However, with the popularization of high performance machine tools and the gradual use of the bearing industry in China, the ceramic bond CBN grinding wheel for bearing inner circle grinding is gradually adopted for the large bearing enterprises in China. The main advantages are: long life, high efficiency, high precision and good roughness.
Two. Common problems and solutions of bearing industry in grinding process:
(1) the formation of spiral line: the main reason for the main reason is that the 1. grinding wheel is untrimmed, the corner is not chamfered, the coolant is not used for dressing; the 2. working table guide guide lubricating oil is too much, which makes the worktable floating; 3. machine tool precision is not good; 4. grinding pressure is too large and so on.
The concrete reason of spiral line formation: 1.V shaped guide rail rigidity is not good, when grinding wheel migration, only the grinding wheel edge and the working surface contact; 2. to repair the ring speed is unstable, the precision is not high, the grinding wheel some edge trimming a little less; 3. the workpiece itself stiffness is poor; 4. grinding wheel has broken too flaking sand and grain on the 4. grinding wheel and The iron scraps under the grinding of the workpiece are attached to the surface of the grinding wheel. For this reason, the dressing should be washed with cooling water or scrubbed clean. The 5. grinding wheel is not good, and there is a local bulge, etc.
(two) the surface appearance of fish scale: the main reason for the surface reproduction of fish scale marks is that the cutting edge of the grinding wheel is not sharp enough, and the phenomenon of "gnawing" occurs during grinding, and the vibration is larger at this time. The specific reasons for the appearance of fish scale marks on the surface of the workpiece are as follows: 1. there are garbage and oil dirt on the surface of the grinding wheel; the 2. wheel is not trimmed round; the 3. grinding wheel is blunt. The dressing is not sharp enough; the 4. diamond fastener is not firm, the diamond is rocking or the quality of the diamond is not good or sharp; the hardness of the 5. wheel is uneven. The main reason for the appearance of hair removal marks on the surface of the working face is that the abrasive particles are sandwiched between the workpiece and the grinding wheel after the coarse grain particles are dropped off.
(three) the workpiece surface is grinded when the surface is grinded: the specific reason is: the traces left by the 1. coarse grinding, the fine grinding is not worn out, the coarse grit in the 2. coolant and the tiny abrasive grains are not clean; the 3. coarse grained grinding wheel is easy to fall off when the grinding wheel has just been repaired; the 4. material toughness validity period or the grinding wheel is too soft; the 5. abrasive toughness and the toughness of the workpiece material fit together. If there is a straight wave mark on the surface of the workpiece, we will cut the cross section of the workpiece through the cross section and enlarge it, and we can see that its periphery is similar to the sine wave. The center of the sine wave is moved around the axis, and the orbit around the sine wave is the wave cylinder, also called polygon.
(four) produce direct waveform trace: the reason is the movement of the grinding wheel relative to the workpiece or the periodic variation of the grinding wheel's pressure on the grinding of the workpiece, which causes the vibration. Such vibration may be forced vibration or self-excited vibration, so the direct wave frequency of the workpiece is often more than one. The specific reasons for the straight wave trace are: 1. wheel spindle clearance is too large; 2. grinding wheel hardness is too high; 3. grinding wheel static balance is not good or the grinding wheel blunt; 4. workpiece speed is too high; 5. transverse Qi knife is too big; 6. grinding wheel spindle bearing wear, with the gap is too large, radial runout; 7. grinding wheel press mechanism or worktable "crawl" and so on.
(five) the surface of the workpiece is burned during the grinding process: the surface of the workpiece is often burned during the grinding process, and there are several types of burns. One is the direction of the burn along the grinding wheel, the dark black patch, and the two is the line or the intermittent line. The surface of the workpiece was burned during the grinding process, and the following reasons were summed up: 1. the grinding wheel was too hard or the size was too fine; the 2. feed was too large, the cutting fluid was not supplied and the heat dissipation was poor; 3. the rotational speed of the workpiece was too low and the speed of the grinding wheel was too fast; the 4. grinding wheel was too large, and the grinding depth was constantly changed; 5. grinding wheel. The dressing is not timely or the dressing is not good; 6. diamond is sharp, the grinding wheel is not good; 7. when the workpiece is rough, the burn is too deep, the fine grinding retention is too small and is not worn off; 8. the clamping force or suction of the workpiece is insufficient, and the workpiece has a stop phenomenon under the action of grinding force. Then how do we know whether the workpiece surface is blackened during grinding? This can be checked by regular acid washing. After pickling the workpiece, it should be inspected immediately under the astigmatic lamp when the surface is moist. The normal surface is uniformly dark grey. If it is a software point, it appears cloudy and dark spots, and the perimeter is not.
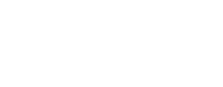
SHANGHAI KEMMER-SHARPEDGING
PRECISION TOOL CO., LTD
Company name: Shanghai Terui Precision Tools Co., Ltd.
Company name: Shanghai Terui Precision Tools Co., Ltd.
Tel:021-68726200 15201970937
Fax:021-68726201
E-mail:ritchie.du@kemmer-sharpedging.com
Web:/
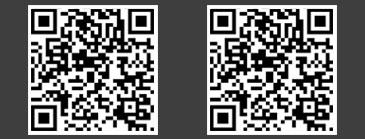
©Shanghai Kemmer-sharpedging Precision Tool Co., ltd